煤化工产业的科技发展状况综述
编辑:2023-06-01 16:31:47
煤矿公司进行研究试验,建有日处理煤50吨的半工业试验装置。
按加氢深度的不同,分为SRC-Ⅰ和SRC-Ⅱ两种。SRC-Ⅰ法以生产固体、低硫、无灰的溶剂精炼煤为主,用作锅炉燃料,也可作为炼焦配煤的粘合剂、铝工业的阳极焦、生产碳素材料的原料或进一步加氢裂化生产液体燃料。近年来,此法较受产业界重视。SRC-Ⅱ法用于生产液体燃料,但因当今石油价格下降以及财政困难,开发工作处于停顿状态。
两种方法的工艺流程基本相似。**初用石油的重质油作溶剂,在运转过程中以自身产生的重质油作溶剂和煤制成煤浆,与氢气混合、预热后进入溶解器,从溶解器所得产物有气体、液体及固体残余物。先分出气体,再经蒸馏切割出馏分油。釜底物经过滤将未溶解的残煤及灰分分离。SRC-Ⅰ法将滤液进行真空闪蒸分出重质油,残留物即为产品──溶剂精炼煤(SRC);SRC-Ⅱ法则将滤液直接作为循环溶剂。固液分离采用过滤,设备庞大,速度慢。近年试验采用超临界流体萃取脱灰法,操作条件:压力10~14MPa、温度450~480℃。以烟煤为原料,SRC-Ⅰ法可得约60%溶剂精炼煤,尚有少量馏分油。SRC-Ⅱ法可得10.4%气态烃、2.7%石脑油及24.1%中质馏分油和重质油
氢煤法 由美国戴纳莱克特伦公司所属碳氢化合物研究公司于1973年开发,建有日处理煤600吨的半工业装置。原理是借助高温和催化剂的作用,使煤在氢压下裂解成小分子的烃类液体燃料。与其他加氢液化法比较,氢煤法的特点是采用加压催化流化床反应器。操作温度 430~450℃,压力20MPa,煤速240~800kg/(h·m3),催化剂补充量每吨煤为0.23~1.4kg催化剂。在以上条件下,约520℃的C4馏分油产率可达干烟煤的40%~50%(质量)。催化剂为颗粒状钼钴催化剂。利用反应器的特殊结构,以及适当的煤粒和催化剂颗粒大小的比例,反应过程中残煤、灰分及气液产物,可以从反应器导出,而催化剂仍留于反应器内,为了保持催化剂活性,运转过程需排放少量已使用过的催化剂(每天约1%~3%),由反应器顶部再补加新催化剂。采用流化床反应器的优点是,可保持反应器内温度均匀,并可利用反应热加热煤浆。由反应器导出的液体产物可用石油炼制方法加工成汽油和燃料油。
2. 间接液化法
煤的间接液化是先将煤气化,生产出原料气,经净化后再进行合成反应,生成油的过程。它是德国化学家于1923年首先提出的,可以分为三大步。
一是制取合成气。把经过适当处理的煤送入反应器,在一定温度和压力下通过气化剂(空气或氧气+蒸汽),使煤不完全燃烧,这样就能以一定的流动方式将煤转化成一氧化碳和氢气混合的合成气,灰分形成残渣排出。
二是进行催化反应。把这些合成气净化,在催化剂作用下,让合成气发生化合反应,合成烃类或液态的烃类的类似石油和其他化工产品。这个过程催化剂起着关键的作用。很早时候,国外有一家公司曾经研制出成分为铁、硅、钾、铜的催化剂,所得产物组成为:汽油32%、柴油21%、石蜡烃47%。
三是需要对产物进行进一步的提质加工。因为经过催化反应出来的油可能有很多指标不合格,如十六烷值含量、硫含量、水分,以及黏度、酸度等,所以还需要把产物进行处理,使其达到合格标准,满足市场需要。
(二)典型“煤变油”生产工艺介绍
1. 俄罗斯煤加氢液化工艺
俄罗斯煤加氢液化工艺:工艺特点:一是采用了自行开发的瞬间涡流仓煤粉干燥技术,使煤发生热粉碎和气孔破裂,水分在很短的时间内降到1.5%~2%,并使煤的比表面积增加了数倍,有利于改善反应活性。该技术主要适用于对含内在水分较高的褐煤进行干燥。二是采用了先进****的钼催化剂,即钼酸铵和三氧化二钼。催化剂添加量为0.02%~0.05%,而且这种催化剂中的钼可以回收85%~95%。三是针对高活性褐煤,液化压力低,可降低建厂投资和运行费用,设备制造难度小。由于采用了钼催化剂,俄罗斯高活性褐煤的液化反应压力可降低到6兆帕~10兆帕,减少投资和动力消耗,降低成本,提高可靠性。
2. 德国煤液化新工艺
德国煤液化新工艺:1981年,德国鲁尔煤矿公司和费巴石油公司对**早开发的煤加氢裂解为液体燃料的柏吉斯法进行了改进,建成日处理煤200吨的半工业试验装置,操作压力由原来的70兆帕降至30兆帕,反应温度450摄氏度~480摄氏度;固液分离改过滤、离心为真空闪蒸方法,将难以加氢的沥青烯留在残渣中气化制氢,轻油和中油产率可达50%。
工艺特点:把循环溶剂加氢和液化油提质加工与煤的直接液化串联在一套高压系统中,避免了分立流程物料降温降压又升温升压带来的能量损失,并在固定床催化剂上使二氧化碳和一氧化碳甲烷化,使碳的损失量降到**小。投资可节约20%左右,并提高了能量效率。
3. 日本NEDOL工艺
日本NEDOL工艺由煤前处理单元、液化反应单元、液化油蒸馏单元及溶剂加氢单元等4个主要单元组成。工艺特点:反应压力较低,只有17兆帕~19兆帕,反应温度为430摄氏度~465摄氏度;催化剂采用合成硫化铁或天然硫铁矿;固液分离采用减压蒸馏的方法;配煤浆用的循环溶剂单独加氢,以提高溶剂的供氢能力;液化油含有较多的杂原子,还须加氢提质才能获得合格产品。
4. 美国HTI工艺
美国HTI工艺是在两段催化液化法和H-COAL工艺基础上发展起来的,采用近十年来开发的悬浮床反应器和HTI拥有专利的铁基催化剂。工艺特点:反应条件比较缓和,反应温度420摄氏度~450摄氏度,反应压力17兆帕;采用特殊的液体循环沸腾床反应器,达到全返混反应器模式;催化剂是采用HTI专利技术制备的铁系胶状高活性催化剂,用量少;在高温分离器后面串联有在线加氢固定床反应器,对液化油进行加氢精制;固液分离采用临界溶剂萃取的方法,从液化残渣中回收重质油,从而大幅度提高了液化油回收率。
(三)我国煤变油技术应用状况
中国早在20世纪80年代就积极开展了相关技术研究。2001年,863计划和中科院联合启动了“煤变油”重大科技项目。中科院山西煤化所承担了这一项目的研究。目前,山东兖矿集团已同时掌握水煤浆与干煤粉两项气化技术,并已在煤的间接液化技术方面取得重大突破,其低温F-T合成煤间接制油技术已达到国际先进、国内领先水平。
(四)云南褐煤资源发展煤变油
作为我国第二大“煤变油”示范项目,先锋项目有先天优势,云南褐煤储量占全国首位,褐煤占全省煤炭总量的60%,该地区出产的褐煤出油率高,活性高。不仅如此,“煤变油”技术需要大量的水,而先锋矿区附近就有水质非常好的淡水湖泊清水海。
1996年,煤炭科学研究总院在全国200多个备选点中选中了云南先锋、神华集团和黑龙江依兰,建设三个示范性的煤变油”项目。
1997年,先锋发45吨褐煤到德国,取得了比较理想的中间试验效果,煤科总院与德方签署了合作进行《中国煤炭直接液化示范厂可行性研究报告》,从此正式启动了云南煤液化厂可行性研究工作。1999年3月,《云南煤液化示范厂可行性研究报告》完成,同年9月,计委主持召开了可研报告研讨会,中德双方进行了比较深入的探讨。2000年先锋煤炭液化项目被列为十五”期间煤炭液化备选项目之一。
CONTACT US
联系电话:+86 13064025178
通信邮箱:3272633465@qq.com
通信地址:山东省济南市槐荫区经七路843号泰山大厦7层C06室
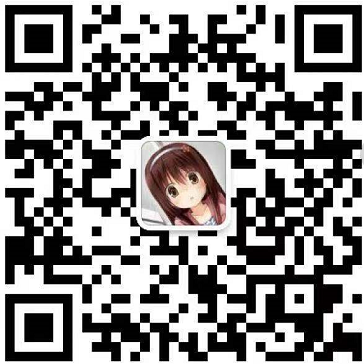
CONTACT US
联系电话:0358-3060341
地 址:山西文水经济开发区68号
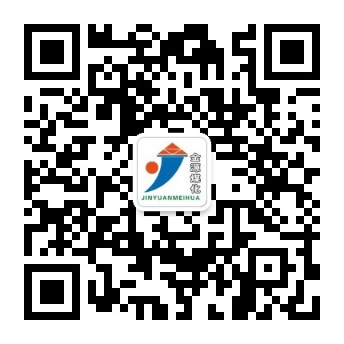
煤化工产业的科技发展状况综述
编辑:2023-06-01 16:31:47
煤矿公司进行研究试验,建有日处理煤50吨的半工业试验装置。
按加氢深度的不同,分为SRC-Ⅰ和SRC-Ⅱ两种。SRC-Ⅰ法以生产固体、低硫、无灰的溶剂精炼煤为主,用作锅炉燃料,也可作为炼焦配煤的粘合剂、铝工业的阳极焦、生产碳素材料的原料或进一步加氢裂化生产液体燃料。近年来,此法较受产业界重视。SRC-Ⅱ法用于生产液体燃料,但因当今石油价格下降以及财政困难,开发工作处于停顿状态。
两种方法的工艺流程基本相似。**初用石油的重质油作溶剂,在运转过程中以自身产生的重质油作溶剂和煤制成煤浆,与氢气混合、预热后进入溶解器,从溶解器所得产物有气体、液体及固体残余物。先分出气体,再经蒸馏切割出馏分油。釜底物经过滤将未溶解的残煤及灰分分离。SRC-Ⅰ法将滤液进行真空闪蒸分出重质油,残留物即为产品──溶剂精炼煤(SRC);SRC-Ⅱ法则将滤液直接作为循环溶剂。固液分离采用过滤,设备庞大,速度慢。近年试验采用超临界流体萃取脱灰法,操作条件:压力10~14MPa、温度450~480℃。以烟煤为原料,SRC-Ⅰ法可得约60%溶剂精炼煤,尚有少量馏分油。SRC-Ⅱ法可得10.4%气态烃、2.7%石脑油及24.1%中质馏分油和重质油
氢煤法 由美国戴纳莱克特伦公司所属碳氢化合物研究公司于1973年开发,建有日处理煤600吨的半工业装置。原理是借助高温和催化剂的作用,使煤在氢压下裂解成小分子的烃类液体燃料。与其他加氢液化法比较,氢煤法的特点是采用加压催化流化床反应器。操作温度 430~450℃,压力20MPa,煤速240~800kg/(h·m3),催化剂补充量每吨煤为0.23~1.4kg催化剂。在以上条件下,约520℃的C4馏分油产率可达干烟煤的40%~50%(质量)。催化剂为颗粒状钼钴催化剂。利用反应器的特殊结构,以及适当的煤粒和催化剂颗粒大小的比例,反应过程中残煤、灰分及气液产物,可以从反应器导出,而催化剂仍留于反应器内,为了保持催化剂活性,运转过程需排放少量已使用过的催化剂(每天约1%~3%),由反应器顶部再补加新催化剂。采用流化床反应器的优点是,可保持反应器内温度均匀,并可利用反应热加热煤浆。由反应器导出的液体产物可用石油炼制方法加工成汽油和燃料油。
2. 间接液化法
煤的间接液化是先将煤气化,生产出原料气,经净化后再进行合成反应,生成油的过程。它是德国化学家于1923年首先提出的,可以分为三大步。
一是制取合成气。把经过适当处理的煤送入反应器,在一定温度和压力下通过气化剂(空气或氧气+蒸汽),使煤不完全燃烧,这样就能以一定的流动方式将煤转化成一氧化碳和氢气混合的合成气,灰分形成残渣排出。
二是进行催化反应。把这些合成气净化,在催化剂作用下,让合成气发生化合反应,合成烃类或液态的烃类的类似石油和其他化工产品。这个过程催化剂起着关键的作用。很早时候,国外有一家公司曾经研制出成分为铁、硅、钾、铜的催化剂,所得产物组成为:汽油32%、柴油21%、石蜡烃47%。
三是需要对产物进行进一步的提质加工。因为经过催化反应出来的油可能有很多指标不合格,如十六烷值含量、硫含量、水分,以及黏度、酸度等,所以还需要把产物进行处理,使其达到合格标准,满足市场需要。
(二)典型“煤变油”生产工艺介绍
1. 俄罗斯煤加氢液化工艺
俄罗斯煤加氢液化工艺:工艺特点:一是采用了自行开发的瞬间涡流仓煤粉干燥技术,使煤发生热粉碎和气孔破裂,水分在很短的时间内降到1.5%~2%,并使煤的比表面积增加了数倍,有利于改善反应活性。该技术主要适用于对含内在水分较高的褐煤进行干燥。二是采用了先进****的钼催化剂,即钼酸铵和三氧化二钼。催化剂添加量为0.02%~0.05%,而且这种催化剂中的钼可以回收85%~95%。三是针对高活性褐煤,液化压力低,可降低建厂投资和运行费用,设备制造难度小。由于采用了钼催化剂,俄罗斯高活性褐煤的液化反应压力可降低到6兆帕~10兆帕,减少投资和动力消耗,降低成本,提高可靠性。
2. 德国煤液化新工艺
德国煤液化新工艺:1981年,德国鲁尔煤矿公司和费巴石油公司对**早开发的煤加氢裂解为液体燃料的柏吉斯法进行了改进,建成日处理煤200吨的半工业试验装置,操作压力由原来的70兆帕降至30兆帕,反应温度450摄氏度~480摄氏度;固液分离改过滤、离心为真空闪蒸方法,将难以加氢的沥青烯留在残渣中气化制氢,轻油和中油产率可达50%。
工艺特点:把循环溶剂加氢和液化油提质加工与煤的直接液化串联在一套高压系统中,避免了分立流程物料降温降压又升温升压带来的能量损失,并在固定床催化剂上使二氧化碳和一氧化碳甲烷化,使碳的损失量降到**小。投资可节约20%左右,并提高了能量效率。
3. 日本NEDOL工艺
日本NEDOL工艺由煤前处理单元、液化反应单元、液化油蒸馏单元及溶剂加氢单元等4个主要单元组成。工艺特点:反应压力较低,只有17兆帕~19兆帕,反应温度为430摄氏度~465摄氏度;催化剂采用合成硫化铁或天然硫铁矿;固液分离采用减压蒸馏的方法;配煤浆用的循环溶剂单独加氢,以提高溶剂的供氢能力;液化油含有较多的杂原子,还须加氢提质才能获得合格产品。
4. 美国HTI工艺
美国HTI工艺是在两段催化液化法和H-COAL工艺基础上发展起来的,采用近十年来开发的悬浮床反应器和HTI拥有专利的铁基催化剂。工艺特点:反应条件比较缓和,反应温度420摄氏度~450摄氏度,反应压力17兆帕;采用特殊的液体循环沸腾床反应器,达到全返混反应器模式;催化剂是采用HTI专利技术制备的铁系胶状高活性催化剂,用量少;在高温分离器后面串联有在线加氢固定床反应器,对液化油进行加氢精制;固液分离采用临界溶剂萃取的方法,从液化残渣中回收重质油,从而大幅度提高了液化油回收率。
(三)我国煤变油技术应用状况
中国早在20世纪80年代就积极开展了相关技术研究。2001年,863计划和中科院联合启动了“煤变油”重大科技项目。中科院山西煤化所承担了这一项目的研究。目前,山东兖矿集团已同时掌握水煤浆与干煤粉两项气化技术,并已在煤的间接液化技术方面取得重大突破,其低温F-T合成煤间接制油技术已达到国际先进、国内领先水平。
(四)云南褐煤资源发展煤变油
作为我国第二大“煤变油”示范项目,先锋项目有先天优势,云南褐煤储量占全国首位,褐煤占全省煤炭总量的60%,该地区出产的褐煤出油率高,活性高。不仅如此,“煤变油”技术需要大量的水,而先锋矿区附近就有水质非常好的淡水湖泊清水海。
1996年,煤炭科学研究总院在全国200多个备选点中选中了云南先锋、神华集团和黑龙江依兰,建设三个示范性的煤变油”项目。
1997年,先锋发45吨褐煤到德国,取得了比较理想的中间试验效果,煤科总院与德方签署了合作进行《中国煤炭直接液化示范厂可行性研究报告》,从此正式启动了云南煤液化厂可行性研究工作。1999年3月,《云南煤液化示范厂可行性研究报告》完成,同年9月,计委主持召开了可研报告研讨会,中德双方进行了比较深入的探讨。2000年先锋煤炭液化项目被列为十五”期间煤炭液化备选项目之一。
CONTACT US
联系电话:0358-3060341
地 址:山西文水经济开发区68号